Equipment and Basic Parameters
- alexdu1122
- Nov 9, 2022
- 9 min read
Equipment List and Basic Parameters
Raw material system
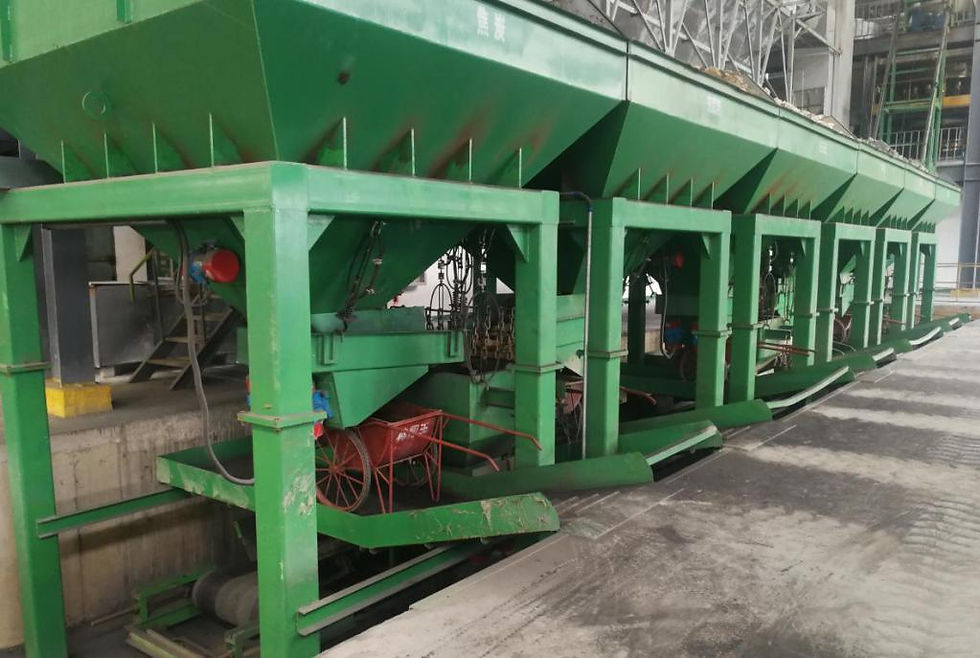
Silo and conveyor
Raw material feeding system adopts six bins; the belt conveyor is used for the transportation of raw material, and the feeding belt is used for feeding batch into the furnace. In production, raw materials will be sent to the respective bin by the loading vehicle and a variety of raw materials will be sent into weighing hopper by a vibrating feeder at the bottom of the bin, and then are charged by belt conveyor after being lift by skip hoist. The whole process is controlled by computer automatically.
Six silos with volume of 8.0 m³ each;
Six belt conveyors for raw material weighing;
Belt conveyors with length of 80m for raw material transmit;
Six vibratory feeders.
Max loading ability: 8t/h.
Melting system

Copula furnace
Cupola is consisted of furnace body, furnace door and opening device.
Made by boiler plate with thickness of 18mm; diameter 1600 mm;
Twenty one combustion tuyeres;
Melting temperature: 1300-1600℃;
Productivity: maximum 6200 kg/h.
Fiber-forming system

Spinning machine
We can provide various options of spinning machines, from traditional open type to the latest Direct Drive type. Four-roll spinner is designed as trolley type, which moves back and forward by motor on rails. Each roller is driven by belt (or shaft directly depends on type), and regulates speed with frequency conversion. Roll bearing uses air-oil lubrication.
The spinning machine is the key equipment of the entire production line and our product is among the best in China with a high fiber formation rate about 70%-80%.
Fiberizing capacity: 4-6 t/h;
Maximum rotation speed: 8000 r/min;
Specialized atomized lubricator;
Binder spraying method: central spraying and ambient spraying
Forming chamber & pendulum system

Drum type collecting system
Drum forming chamber is used for rock wool collection.
Diameter: 5 m;
Drum linear speed: 50m-120m/min;
Net plate length: 2420 mm; net plate width: 1423 mm, totally 11 net plates;
The negative-pressure system helps to achieve a more uniform collection of rock wool through the forming chamber; the net plate angle is no less than 80° and the width of stone wool is more than 2200mm. Density of single-layer rock wool is no higher than 450 g/m²;
The forming chamber is equipped with automatic slag-removal system to reduce the shot content to meet the requirement of national standard, that is, less than 10%;
Noise is less than 85 db. (Measured 1 meter away from the machine)
Two-section lift type weighing shaping conveyor
Two-section lift type weighing shaping conveyor
By swing belt, primary mat is made into secondary mat in multi-layers with certain thickness and density on the forming conveyor.
Forming conveyor is mainly consisted with actuator, tensioning gear, lifting gear, baffling device and frame.
Maximum felt width: 1450 mm;
Linear speed: 1.8-18 m/min, adjustable; frequency: 9-90 Hz;
The conveyor has weighing system on both ends;
Pendulum transport system

Pendulum
Pendulum is consisted with belt conveyor, one swing belt, one swing structure, and pendulum platform.
Pendulum conveyor is used to receive primary mat from fiber collection machine. Primary mat is then sent to swing belt by belt conveyor. By the back and forth of swing belt, primary mat is made into multilayer blanket on the forming conveyor.
Operating/working width: 2500 mm;
Maximum speed: 120 m/min;
Driving motor power: 18.5 kW.
Four-meter weighing conveyor
Maximum felt width: 1450 mm
Linear velocity: 1.8-18 m/min, adjustable; frequency: 9-90 Hz;
Equipped with four weighing modules.
Crimping machine
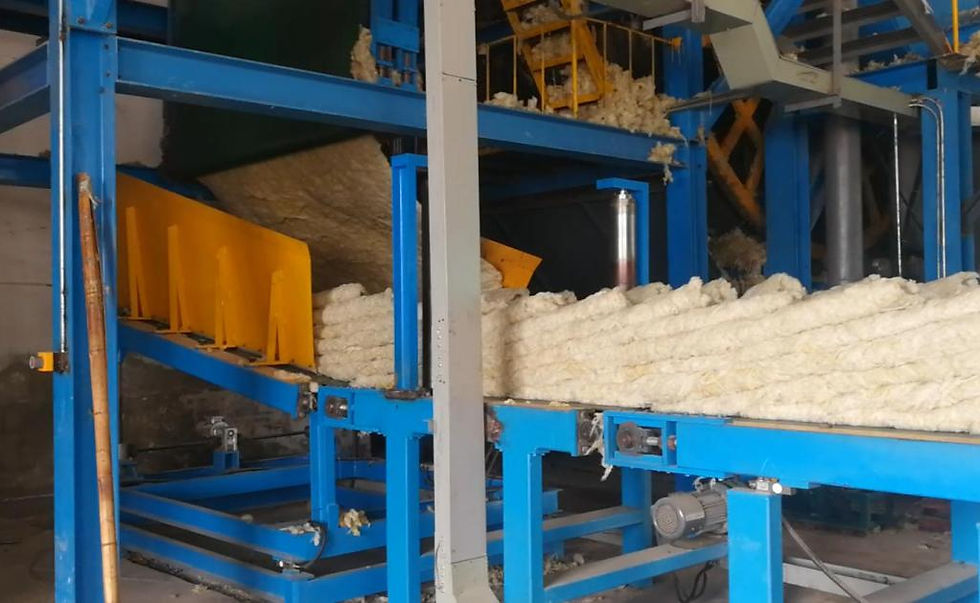
Crimping machine
Crimping machine is consisted of several fixed down roller beds and five lifting upper pressing roller beds. According to the product specification, distance between up and down roller and inlet angle of crimping machine can be adjusted.
Crimping machine compresses secondary mat longitudinally, which improves product strength.
Maximum crimping ratio: 1:4;
Maximum felt width: 1450 mm;
Linear velocity: 1.8-18 m/min, adjustable; frequency: 9-90 Hz;
Installation width: 2768 mm;
Total length: 4000-4500 mm
Working surface elevation: 1100 mm
Motor power: 4 kW, totally 8 motors.
Pressing machine

The pressing machine is used to press secondary mat from crimping machine further, and send it into curing oven. One fixed down roller bed and one lifting up roller bed. According to the product requirements, up and down roller beds are driven separately. Pressing machine can move sideways integrally and have lock device, which are used to move sideways and get space when maintaining.
Maximum felt width: 1460 mm;
Installation width: 2140 mm;
Total length: 1800 mm
Linear velocity: 1.8-18 m/min, adjustable; frequency: 9-90 Hz;
Totally 3 motors, including transmission type and lift type are equipped, and among which two are variable frequency motors with power of 4 kW and one is motor with power of 2.2 kW;
Working surface elevation: 1100 mm.
Curing oven(4 zones)
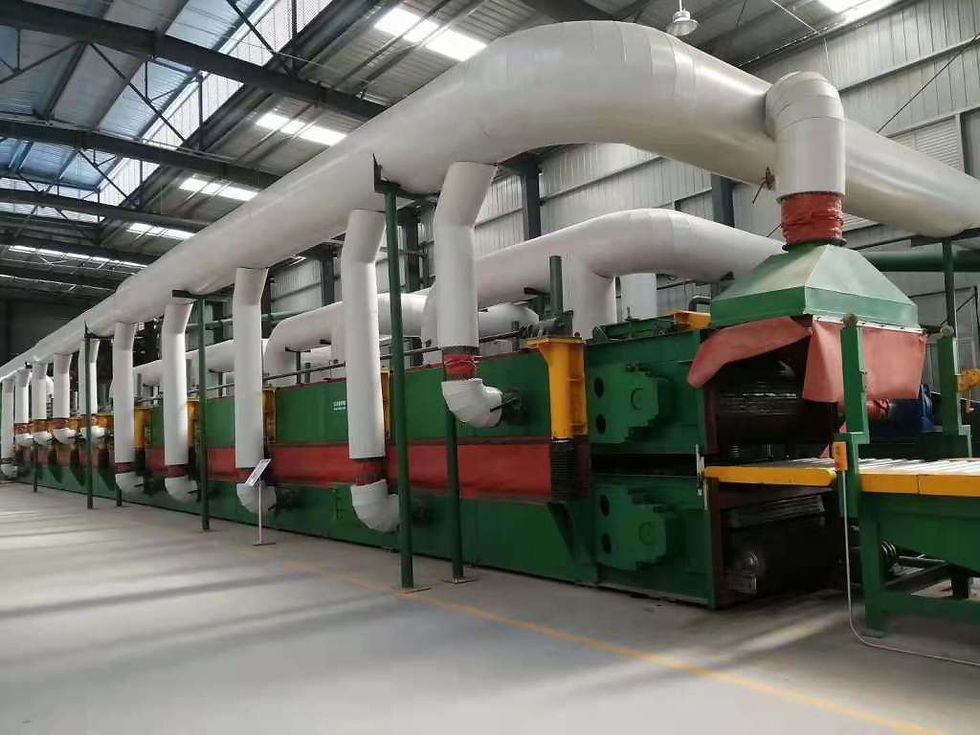
Curing oven
Usage and range of application
The mat entering the curing furnace is conveyed and pressurized by the upper and lower conveyor belts, and at the same time, the hot air is blown in for drying, so as to form a certain thickness of products.
Operating principle
Inner curing oven has multi air chambers. Each chamber has special seal structure with chain and flights. And there are also seal structure between air chambers and flights. The seal structure can avoid heat air short circuit and improve curing efficiency.
Main drive of curing oven is consisted with two driven systems, which are used to drive up and down conveyor separately.
The upper and lower parts of the outlet end are respectively provided with brush rollers to clean the flight.
Technical indexes
a) Felt width: 1400 mm;
b) Lifting distance of upper chain plate: 10-300 m;
c) Top bridge lifting speed: 20 mm/min;
d) Curing chamber size: 34.565 m*2.055 m*2.4 m;
e) The reducer brand is Tailong, and the motor brand is Dazhong;
f) In curing chamber, the vertical net plate is made of steel plate of 16 mm thickness, and the panel is made of plate of manganese with thickness of 4.5 mm;
g) Linear velocity: 1.8-18 m/min, adjustable; frequency: 9-90 Hz;
h) Curing capability, KT value is 4000-20000;
i) Minimum felt thickness: 30 mm.
6-meter cooling conveyor
Cooling conveyor
Forcibly cool wool boards or mats from curing oven.
Maximum felt with: 1460 mm
Linear velocity: 1.8-18 m/min, adjustable; frequency: 9-90 Hz;
Working surface elevation: 1100 mm;
Driving motor power: 4 kW.
Slitting conveyor
Six-head slitting units
Slitting units are used to cut the boards transmitted from the curing oven in half according to requested width, and totally 6 cutting head equipped (among which 3 are backups).
Linear velocity: 1.8-18 m/min, adjustable; frequency: 9-90 Hz;
Slitting width: 600×2=1200 mm, adjustable;
Maximum product thickness: 200 mm;
Totally 6 air cylinders are adopted to lift and lower the saws;
Totally 6 motors with power of 4 kW are employed to convey the saws;
One variable frequency motor with power of 3 kW is used for the conveyor;
Maximum machine width is 4300 mm (including ladder);
Total length: 3700 mm; working surface elevation: 1100mm;
Equipped with six dust collecting covers.
Edge trimming conveyor
Edges trimming unit
Edge trimming machine: two edge trimming machines are installed each side, which can move transverse. Edge trimming machine uses fixed dead knife and rotate fly-cutter roll to complete edge trimming function.
The waste edge, cut from lengthwise conveyor, is cut into particle by rotate knife of edge trimming machine, and then is sent into fiber collection machine for reuse by air delivery system. And meanwhile, complete product transportation.
Linear velocity: 1.8-18 m/min, adjustable; frequency: 9-90 Hz;
Lateral movement distance: 180 mm;
Maximum edge width: 200 mm;
Two motors with power of 3 kW for transmission of knife rollers;
Knife roller diameter: 280 mm;
Total machine length: 3000 mm, working surface elevation: 1100 mm;
A variable frequency motor with power of 3 kW is equipped with the conveyor;
Maximum edge thickness: 200 mm.
Granularity: less than Φ10 mm
Length measuring device
Length measurement system
The length counter in the length measuring device collects and outputs signals to realize the length cutting of products by CNC flying saw and swing saw.
Mainly used for the measurement of rock wool needed to be cut with the help of coder with 130,000 pulses providing signal to flying saws and transverse cutting unit.
CNC flying saw (tracking cutting speed 20 meters)

Double-blade CNC flying saw
Cross cutting machine is installed on the upper part of belt conveyor, and is consisted with saw frame, which can move transversely, and travelling crane consisted with bottom dust collection frame, which can move lengthwise. Servo control is used for horizontal cutting and synchronization of flying saw with production line.
Technical indexes:
Maximum cutting thickness: 250 mm;
Maximum cutting width: 1400 mm;
Tracking cutting speed is no less than 28 m/min;
Tracking cutting speed of single-blade is no less than 18m/min, and that of double-blade is no less than 25 m/min;
Cutting accuracy is less than the requirement of national standard (±2mm);
Dust collecting box is equipped;
Operating surface elevation: 1100 mm;
Power of conveyor motor: 4 kw
Mitsubishi servo motor is adopted.
Roller conveyor between flying saw
The role of belt conveyors in the production line on the one hand is working as the transition section for various machines and connecting production processes to achieve the orderly running of the production line, and on the other hand via different speeds providing time with packaging for final products at the end of the line.
Maximum felt width: 1460 mm;
Linear velocity: 1.8-18 m/min, adjustable; frequency: 9-90 Hz;
Operating surface elevation: 1100 mm.
Dust collection belt conveyor
Dust collection conveyor
Maximum felt width: 1460 mm
Linear velocity: 1.8-18 m/min, adjustable; frequency: 9-90 Hz;
Power of conveyor motor: 3 kW;
Unit for board dust collection is equipped.
Electronic control system
Combustion and heat-exchange system

Heat-exchange and combustion system
The temperature of hot wind needed by copula furnace (exit of heat exchanger) is 500~600℃ (one furnace cycle, within about 15 days), air volume 6 000 Nm³/h, maximum pressure in the exit of heat exchanger: 8000 Pa. The temperature needed by curing chamber is 250~300℃ (end gas of 260℃ is considered), and air volume is 12 000 Nm³/h. Control mode: manually and automatically; fuel: natural gas, heat productivity: ≥8300 kcal/Nm³.
Technical parameters of mixed heating furnace for dedicated for rock wool production
a) The heating modes for copula furnace and curing chamber are heat-exchanged conversion;
b) The temperature of hot wind for copula furnace is 500~600℃ (one furnace cycle, within about 15
days), and that for curing chamber is 250~300℃ (end gas of 260℃ is considered), and air volume is 12 000 Nm³/h;
c) Hot wind stability: setting temperature: ±10℃;
d) Fuel: Natural gas; heat productivity: ≥8300 kcal/Nm³; pressure: 15~30 KPa.
Desulfurization system

Desulfurization system
The smoke blowed by induced draft fan into desulfurization tower goes up evenly from the lower middle (flow velocity is 2.5 to 3.2 m/s) and in turn goes through high-density spray washing reaction zone and absorption reaction zone formed by three-level spray system. The solution via spiral nozzle produces fine droplets, which provide large contact area to mix completely with flue gas flow and allow sufficient physical and chemical reaction of character and thermo-exchange between gas and liquid. Droplets absorb SO2 and catch dust particles when fall down, so as to achieve efficient removal of SO2. The caught dust particles down flow into the bottom of desulfurization tower and will be discharged from the overflow aperture into setting pond.
Desulfurized smoke continues to rise, and after striking the folded plate of the first-level dehydration mist device equipped in the desulfurization tower for many times, it turns into bigger droplets which will fall after its separation with smoke, and the smoke goes out through the upper cylinder cone part, and the whole dust removal desulfurization process is completed. The waste liquid containing dust is discharged into the sedimentation tank through the overflow hole at the bottom of the barrel (the overflow hole is designed with water seal to prevent air leakage and equipped with cleaning hole to facilitate the cleaning of the bottom of the barrel), and will be recycled after precipitation (ash removal) and alkali addition (regeneration).
Technical index of purified smoke
No. Item Before After Description
1 Ringelman emittance Level II-III Less than level I Performance: 0
2 SO2 concentration Provided by buyer ≤100 mg/m3 Performance:80 mg/m3
Resin system
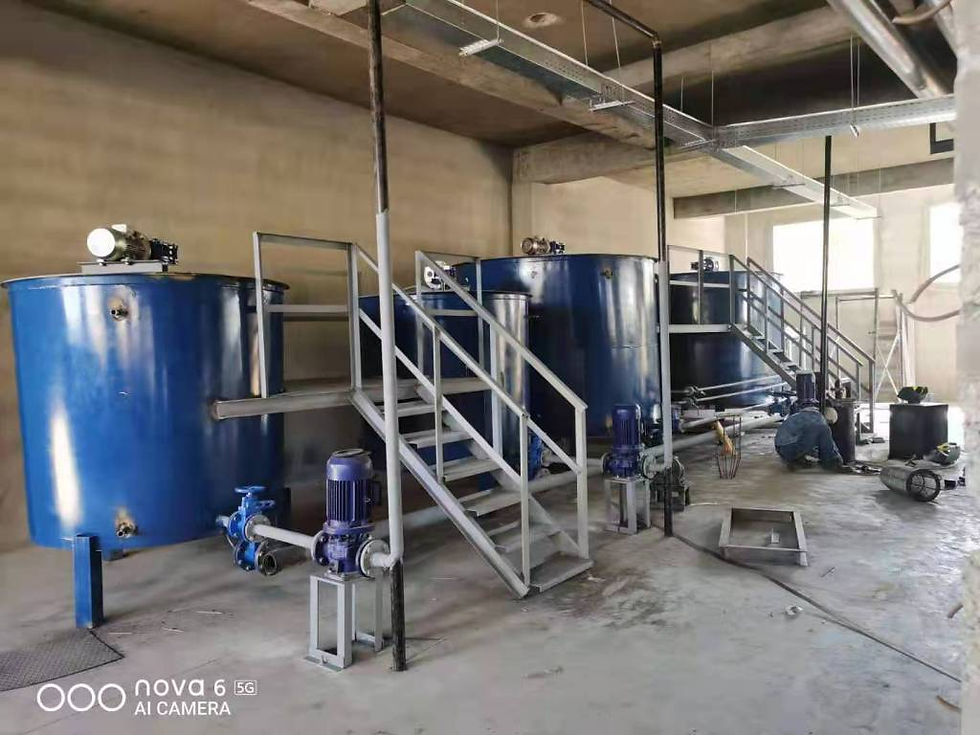
Resin system
The binder system in rock wool line is used for storage and blending only.
Parameters depends and can be customized according to actual needs.
Fan
Air compressor
Dust collecting system

High temperature bag-filtering dust collector:
Standard equipment, operating temperature is controlled at 150~220 degrees. If the temperature is too low, water vapor condensation absorbed, resulting in poor dust removal effect of cloth bag, and if temperature is too high, cloth bag would be damaged.
Range area 550m2, air volume 35000m2. It could remove more than 99% of dust and other particles.
It also contains bypass control and pneumatic bypass valve. When the temperature is higher than 240 degrees, the exhaust gas will enter the desulfurization system directly, rather than through the cloth bag.
Normal temperature cutting dust collector:
Bag-type dust collector ,120m2, fan 22 kw.
Range area designed according to 120m2, considering the low density of dust, the collector shell volume is doubled.
Dust removal efficiency:
Above 0.2 micron , 99%;
Above 1.0 micron, close to 100%.
Water system
Cooling tower
Double station packing machine

The packaging unit is the final part of rock wool production line. The production process finishes with the packaging of the material.
Hairui proposes different packaging systems to meet the needs expressed by the customers.
At the stacker discharge the packs are automatically wrapped in polythene and thermo-shrinked.
During the packaging the packs, depending on the density, can be compressed, reducing its volume, so reducing the transportation costs.
Packing size for rock wool boards (length*width*height):
1200×600×(30~200)mm
Products density for available packing(except for mats and soft board):
40-200 kg/m3
Maximum packaging speed:
8 packages/min
Power:
80 kW
Thank you!
Comments